Whether it’s a week’s vacation in New Orleans or a quick overnight business trip in Boise, hotel laundry could be considered the great equalizer. No matter the destination or the length of stay, clean, crisp sheets and fluffy towels are nonnegotiable when it comes to guest satisfaction.
“Properties provide many amenities, but all hotels provide one thing—a bed. A property can deliver the highest level of services, the most beautiful lobby and more, but if the guest encounters rough, wrinkled, stained or overall poor-quality bed linens or bathroom towels, satisfaction takes a hit that will show in online reviews,” said Randy Radtke, content and media relations manager for Alliance Laundry Systems. “Viewing the laundry as a back-of-the-house function is a mistake.”
Increasing efficiency and productivity can be a challenge, but experts suggest a few ways to make the most of your laundry operation.
“Sometimes, the simplest process adjustment can have the greatest impact,” Radtke noted. “One way to ensure efficiency is to make sure staff are trained on what full loads look like. Underloading equipment wastes labor, utilities and chemicals.”
Equipment selection accounts for 13-15 percent of cost drivers for hotel laundry operations, according to Xenia, a software solution for hotel laundry management. The right machines can make a big difference in the bottom line.
“Efficiency comes with equipment choice and the ability to clean faster with less water, electricity and natural gas,” said Joel Jorgensen, vice president of sales for Girbau North America. To do this, he recommends replacing top-loading washers with front-loading machines. “Front-load washers produce two to three times more extract (spin speed) than top loaders, so the time and energy consumed in the drying process is slashed by half or more. The frontloads remove more moisture with the high spin, which in turn cuts drying time and associated natural gas costs.”
In addition to load size, machine size is key.
“Undersized equipment limits cleaning abilities, which can leave stains or foreign debris left on linens, or cheaper equipment brands can lead to mechanical malfunctions and service stoppages,” said Joe Fleming, national sales manager for Yamamoto. “Oftentimes this leads to overtime payments while running lesser equipment for longer hours and/or delays in turning rooms for incoming guests.” Jorgensen agreed, saying that regular preventative maintenance is critical to keep machines running at peak efficiency.
“Whether over- or under-sized, both result in unforeseen costs, which can be difficult (and pricey) to overcome. After the design and build phase, walls and utilities are in place, which makes it difficult to properly retrofit if needed,” Fleming added.
RFID tracking of linens is a growing trend in the outsourced laundry sector, and for good reason: Entire inventories can be tracked with just a few keystrokes. Laundris Corp. first applied its RFID technology to hotel laundry services, tracking inventory for over 100,000 items at select properties. Items are tracked by scanners to precisely analyze inventory usage patterns.
“Accurate tracking of inventory and efficient reordering can lower related operational costs up to 30 percent,” said Don Ward, Laundris founder and CEO. “An inventory-management platform will prove a game changer for properties of any size.”
Laundry: the Key to Customer Satisfaction
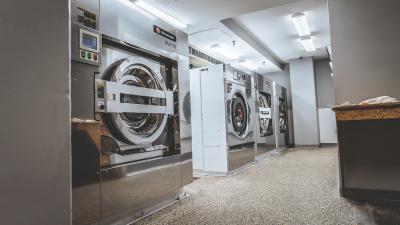
There are only a handful of ways to differentiate yourself in hospitality,” Fleming said. “Varying services and amenities are all great, but no matter which brand a guest is staying with, a large portion of their time will be spent in a bed. The quality of the bed experience plays a huge role in customer satisfaction.” He suggests the following considerations to reducing your hotel laundry operations costs:
- Utilize equipment with High-G (300G or more) extract. This will reduce cycle times in a washer and a dryer, ultimately saving you labor hours and utility costs.
- Size your equipment properly. This will control utilities costs while giving you the best throughput per labor hour, regardless of the busy or calm seasons.
- Choose a higher quality equipment brand. Reduced service and repair costs almost always lead to lower lifetime cost on equipment in the long run.
Some commercial washers remove significantly more water from each load, according to Girbau North America. When drying can be eliminated and linens can be fed directly from the washer to ironers, hotels can cut 20 to 40 minutes off processing time—maximizing production and saving costly labor and energy.